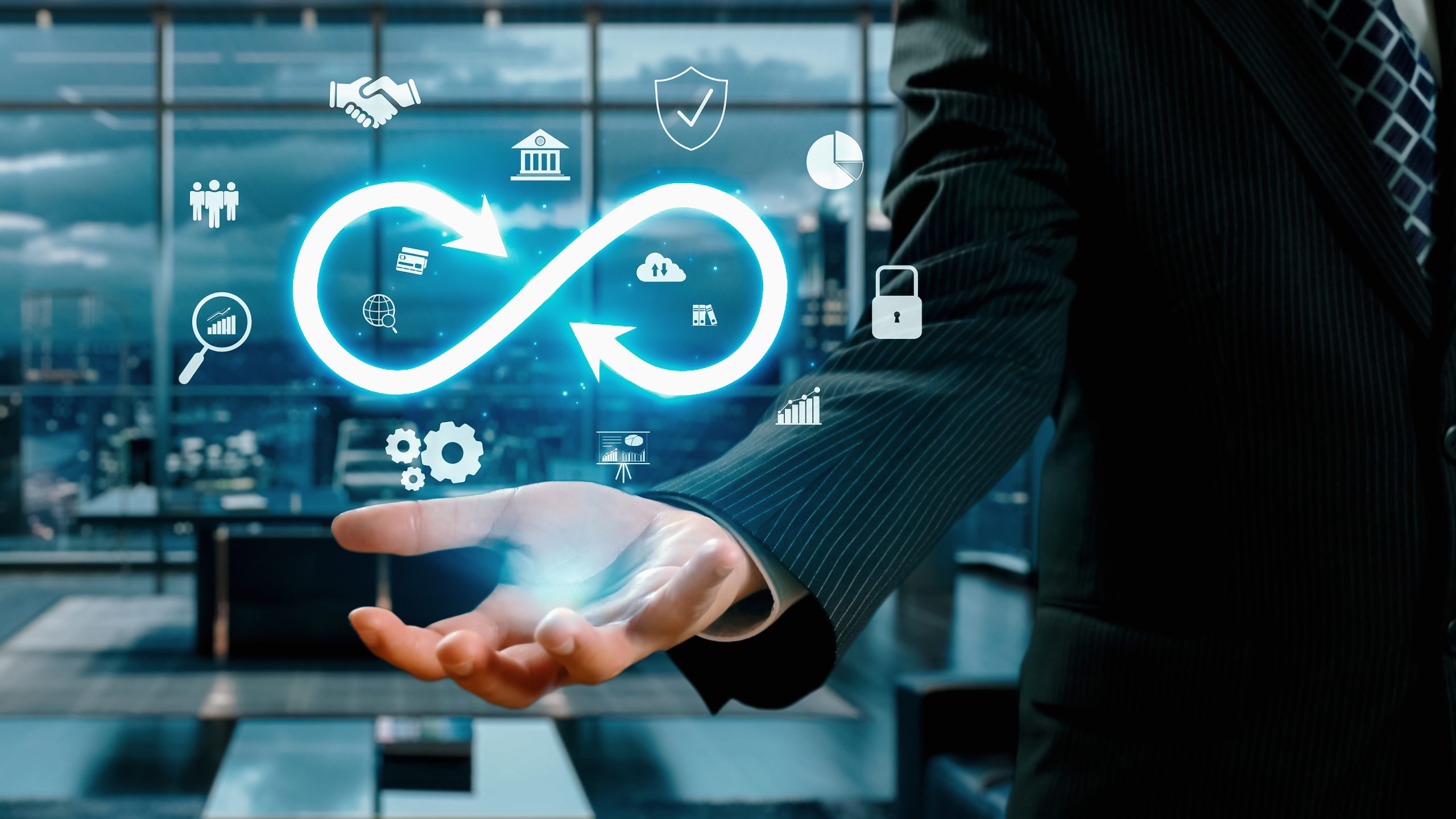
- By qematicadmin
Lean and Six Sigma: What’s the Difference and Why It Matters for Your Business
In today’s competitive landscape, businesses across industries are striving to optimize performance, reduce costs, and deliver consistent quality. Two of the most powerful methodologies that support these goals are Lean and Six Sigma. While often used together, they are fundamentally different in approach. Understanding the difference between Lean and Six Sigma can help you apply them more effectively to your operations.
What is Lean?
Lean is a methodology focused on eliminating waste and improving process speed. Originating from Toyota’s production system, Lean emphasizes delivering value to the customer by cutting out non-value-added activities.
Key Principles of Lean:
- Value Stream Mapping – Visualizing processes to identify waste
- Eliminating Waste (Muda) – Reducing excess inventory, waiting time, overproduction, etc.
- Continuous Improvement (Kaizen) – Small, ongoing changes for long-term efficiency
- Just-in-Time Production – Making what is needed, when it’s needed
Goal: Maximize customer value with fewer resources.
What is Six Sigma?
Six Sigma is a data-driven methodology aimed at reducing process variation and defects. Developed by Motorola and widely adopted by global enterprises, it uses statistical tools and project-driven frameworks to ensure quality and consistency.
Key Concepts in Six Sigma:
- DMAIC Framework – Define, Measure, Analyze, Improve, Control
- Statistical Process Control (SPC) – Monitoring variation with data
- Focus on Defect Reduction – Targeting a maximum of 3.4 defects per million opportunities
- Quality Improvement Projects – Led by certified experts (Yellow, Green, Black Belts)
Goal: Improve quality by eliminating variability and defects.
Lean vs. Six Sigma: What’s the Difference?
Feature | Lean | Six Sigma |
Main Focus | Waste elimination | Defect reduction & process variation |
Approach | Visual, workflow-based | Data-driven, statistical |
Speed of Implementation | Often quicker | Requires more time, analysis |
Best For | Reducing cycle time, costs | Improving quality, accuracy |
Tools Used | 5S, Kanban, Kaizen | DMAIC, SPC, Control Charts |
Can Lean and Six Sigma Work Together?
Yes! Many companies combine both into a Lean Six Sigma approach. This hybrid strategy blends Lean’s efficiency with Six Sigma’s precision, offering a comprehensive toolkit for process improvement.
Benefits of Lean Six Sigma:
- Increased operational efficiency
- Reduced costs and waste
- Improved product and service quality
- Better customer satisfaction
- Scalable improvements across departments
Why Choose Qematic for Lean & Six Sigma Implementation?
At Qematic, we help businesses unlock measurable improvements using proven Lean and Six Sigma methodologies. Whether you need to streamline workflows, reduce defects, or train your teams with Lean Six Sigma certifications, we offer tailored solutions designed to scale with your goals.
Our Services Include:
- Lean & Six Sigma Consulting
- DMAIC and Kaizen Project Facilitation
- Process Audits & Value Stream Mapping
- Lean Six Sigma Training & Certification
Final Thoughts
Understanding the difference between Lean and Six Sigma is the first step toward operational excellence. When used strategically—individually or together—they become powerful tools for driving transformation, especially in sectors like manufacturing, engineering, logistics, and supply chain management.
Want to get started?
Contact Qematic today to see how Lean and Six Sigma can reshape your business performance.