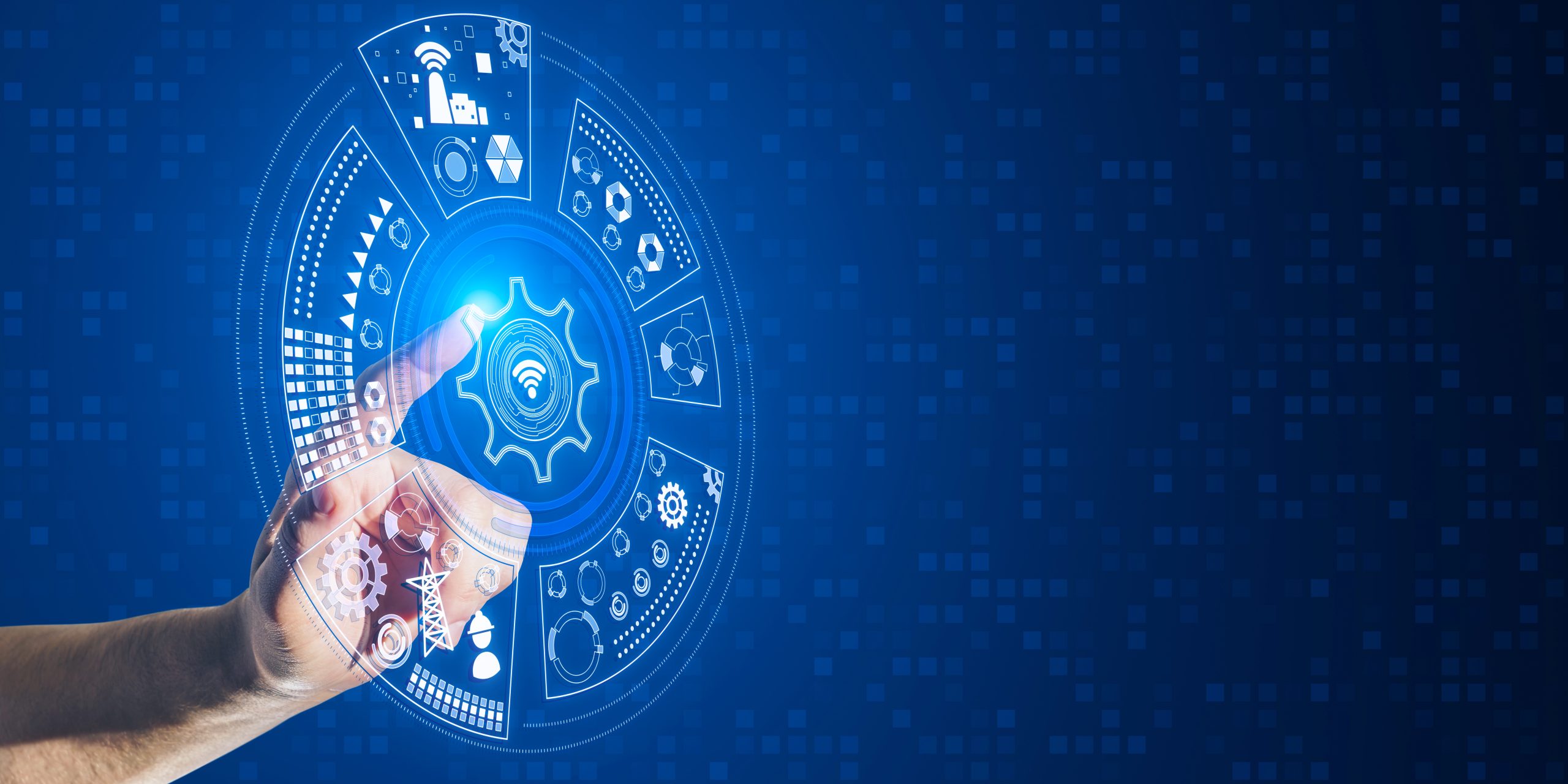
- By qematicadmin
In today’s fast-paced business environment, achieving operational efficiency is critical for sustainable growth. Whether you’re launching a new product or refining an existing system, integrating the principles of 5S with engineered process design can create a significant competitive advantage.
At Qematic, we help businesses leverage proven frameworks and modern tools to streamline operations, reduce waste, and enhance productivity. One of the most effective combinations we use is 5S and optimized process design.
Understanding 5S in Process Design
The 5S methodology is a workplace organization system originating from Japan, designed to eliminate waste and ensure continuous improvement. The five pillars of 5S include:
Sort – Remove unnecessary items from the workspace
Set in Order – Arrange tools and materials for efficient access
Shine – Maintain cleanliness for safety and efficiency
Standardize – Establish procedures and best practices
Sustain – Maintain discipline to uphold improvements over time
When applied effectively, 5S supports the foundation of strong, scalable, and safe process design.
Why Combine 5S with Process Design?
While 5S focuses on workplace organization, process design emphasizes the flow of activities, resources, and people. Combining the two results in systems that are not only clean and structured but also optimized for performance. Key benefits include:
Improved task flow and production timelines
Enhanced safety and compliance
Standardized quality output
Reduced operational costs
Increased employee efficiency and morale
The Role of Engineered Process Design
Process design is a strategic approach to defining, analyzing, and improving how tasks are executed. At Qematic, our engineering experts map existing workflows, identify pain points, and restructure processes to maximize efficiency and minimize resource wastage.
This includes:
Process mapping and analysis
Task sequence reorganization
Layout and space planning
Digital transformation integration
Performance metric development
By aligning these efforts with 5S principles, we ensure that processes are both technically optimized and practically sustainable.
Application in Manufacturing and Engineering Environments
Consider a manufacturing unit where delays, errors, and clutter are frequent. By applying 5S and process redesign, the workspace is cleared of redundant tools, the layout is realigned for logical flow, and tasks are standardized with visual cues. These changes not only speed up production but also create a safer and more consistent working environment.
Companies often see improvements such as:
30 to 40 percent increase in output efficiency
Shortened lead times
Lower defect rates
Easier training and onboarding processes
Qematic’s Approach to 5S and Process Optimization
We approach every project with a data-driven, consultative mindset. Our services include:
5S audits and training
Process design consultations
Facility and workflow redesign
Lean implementation
KPI setup and tracking tools
We partner with engineering and manufacturing firms to create practical solutions that deliver measurable results.
Conclusion
Implementing 5S alongside engineered process design is a strategic move toward sustainable operational excellence. It brings order to complexity, clarity to processes, and value to every step of production.
If you’re ready to transform your workflows and drive better outcomes, Qematic can help you build and sustain a smarter, leaner operation.